MTA Q&A with Gaggiano Custom Panel & Paint
With a quality collection of beautifully restored muscle cars of his own, Jerry Gaggiano knows beautiful cars. It’s no wonder then that his custom paint and panel shop in Ingham, North Queensland is growing each year.
WORDS & PHOTOS: LARA WILDE
What products and services do you offer at Gaggiano Custom Panel and Paint?
JG: Our core business is insurance claims for panel repair and paint work. We also do private panel and paint work ranging from cars, to motorbikes, tractors, boats, race cars, restorations and coffins.
There is a massive focus on 4X4 gear, from the supply and fitment of accessories and products such as suspension, through to providing rustproofing services.
We work with a lot of people who are serious about off-road and 4X4 and want to maintain and improve their vehicle of choice. We feel the motoring industry has been naturally moving in that direction for a long time and as people get more serious about their off-road rig, we’re there to provide solutions for them.
Whoa . . . you do panel and paint work on coffins?
JG: Yes, we colour customise coffins for the local undertaker. We always say there is no job too big or too small.
Do you do anything else?
JG: We are the RACQ preferred centre for windscreen replacements for Ingham which gives us credible introductions to a new customer base. Finally, just to keep us busy, we provide a sandblasting service for a wide variety of projects.
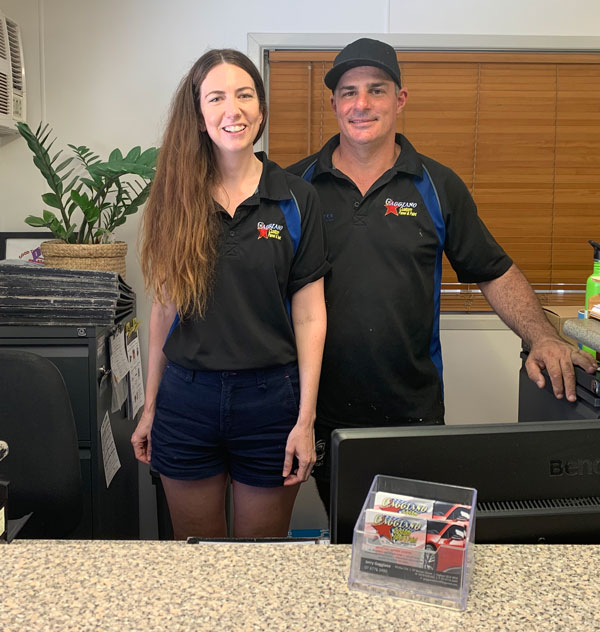
Jerry Gaggiano with fiancé Melanie.
In your personal collection you have some beautiful cars. Do you get to work on old-school restorations?
JG: We usually have at least two restorations booked in at the workshop at any one time.
When did it all start?
JG: In 1994, when I was 16, I started my apprenticeship as a Spray Painter with Gianotti’s Custom Panel & Paint. I went on to purchase the business from Dave Gianotti in 2005 and completed my trade qualification as a Panel Beater in 2013.
Are you still hands on in the business today?
JG: You’ll find me in the workshop every day on the tools and managing workflow. I also prioritise talking with and listening to customers throughout the day.
A typical day at work includes quoting on jobs, spending time talking to and listening to customers, liaising with insurance assessors, spray painting cars, panel beating cars, working with the apprentices to teach and guide them, managing the workflow of the business and then monitoring the logistics and staying on top of orders for paint and consumables in the workshop.
Who is your current team?
JG: At the moment we have six staff on the team including myself as a business owner and qualified spray painter and panel beater. My fiancé Melanie runs the office for me and makes sure that our customers are well taken care of. I really appreciate having a business where I can go to work with my partner every day.
Karl is our qualified panel beater on staff and Nicholas is our apprentice panel beater. Kevin is our qualified spray painter and at the moment we have Brandon as the spray painter’s labourer but soon he will be signing up to do his apprenticeship. We are a well-rounded team and everyone works well together.
We have a succession plan in place, training apprentices in our business to deliver the quality of work and level of customer service that our client base expects.
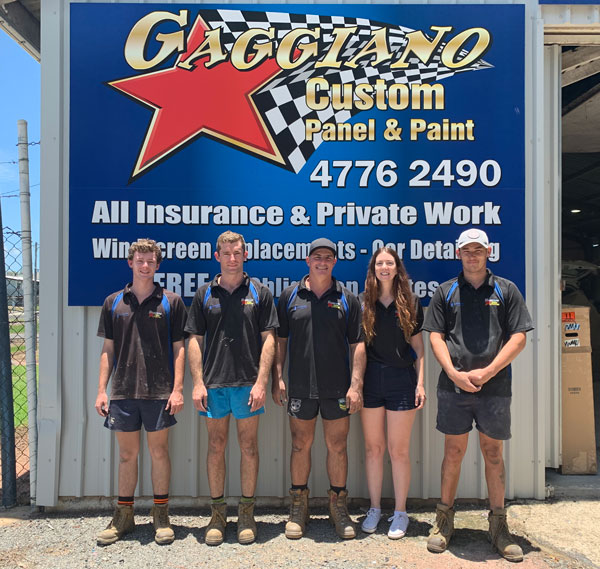
The Gaggiano Custom Panel and Paint team
What are your plans for the next few years?
JG: To continue to be consistent, reliable and provide quality workmanship.
What advice would you give to a young you starting out in the industry?
JG: Dear young Jerry, you should have bought 20 Ford XY GT Phase 3’s (ha ha ha!)
How much importance do you place on social media for your business?
JG: We recognise that social media can be a good marketing tool at times, but we rely on our reputation to speak for itself and aim towards giving customers an experience where they feel they will happily merge into our repeat customer base.
What do you see as the greatest advancement in technology for your business?
JG: It is hard to pinpoint any one thing in particular. The efficiency that goes hand in hand with upgrading to any modern form of technology, from the office to the workshop, is always appreciated. The challenge is always being open to change and having the time to integrate the new technology into the day-to-day business.
What cars do you own?
JG: A 1972, two-door Holden HQ Monaro with a 420 cubic-inch small block producing 770 horsepower and a 1968, four-door Chevy Camaro with 468 cubic-inch big block Chev producing 650 horsepower. I have owned many cars including a top performing Holden Statesman drag racing car which still competes locally.
What has been the greatest benefit of your MTA Queensland membership?
JG: I first joined MTA Queensland when I bought the business in 2005. We really like knowing that we have support in our business when we need it. MTA Queensland is a great resource-base for any questions that we have from the latest advancements in industry technology through to HR matters.
What do you do with your spare time?
JG: Living in Ingham means the fishing is great and almost every weekend my fiancé Mel and I are somewhere local near or on the water with a line. We also have a property out of town that requires upkeep and attention. And of course, I spend time working on my own cars and boats.
Source: Motor Trader E-Magazine (March 2020)
11 March 2020